Operation and Maintenance
With engineering expertise and know-how accumulated within the company over the years, we render our services for such areas as operation upgrade, debottlenecking, and trouble-shooting for the plants in operation, adding value to the Project in the following respects.
Process Improvements
Since its foundation, Chiyoda has constructed, both within Japan and overseas, a large number of plants relating to the fields of energy sources such as petroleum and natural gas, petrochemicals and chemicals, pharmaceutical products, and general production facilities etc. At the same time, using the abundant expertise and experience cultivated over our many projects, we also offer proposals for improving the efficiency of production in the plants that are of such importance to our customers.

- Proposals for improvement of, or application of new technology to, individual equipment and machines
- Proposals for capacity enhancement or increased energy efficiency in a process unit
- Proposals to increase mutual energy efficiency between multiple process units and utility systems
-
Proposals to increase the production efficiency and energy efficiency of the whole industrial complex (i.e. amongst multiple plants)
-
Proposals for capacity enhancement, production efficiency and energy efficiency through the introduction of leading edge technology
Improvement of Utility System
The efficiency of utility system can be improved by review and modification as same as that for process unit. Chiyoda proposes the improvenment based on the experience for design and construction of utility system for the field of electricity, water treatment, heating medium including steam system to enable the efficient of the system for the saving energy.
Power System : Optimization and improvement of existing power system
Water System : Re-use of waste water
Heating Medium System : Energy saving by Pinch Technology
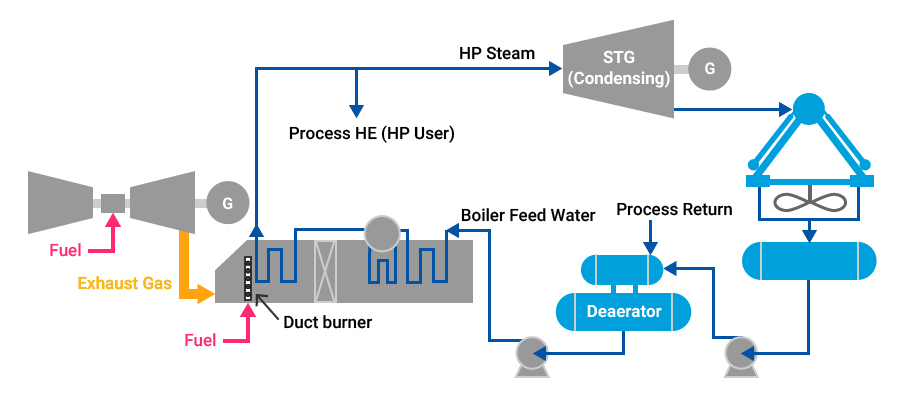
Improvements in Equipment Reliability
For the safe operation of plant equipment and the provision of a stable supply of products, suitable performance of reliability-based design for plant equipment, and the extent to which it can be maintained and managed, have become of great importance. In particular, with respect to concerns regarding the overaging of existing plant equipment in recent years, suitable diagnosis and assessment of the soundness of the equipment, and the extent to which suitable measures and management are carried out for those parts causing reliability concerns, have become major issues. At the level of individual issues and requests relating to the plant equipment so important to our customers, we prepare and implement an improvement/solution plan that utilizes the latest and best technology relating to plant equipment diagnosis, analysis engineering services, advanced equipment condition monitoring and equipment management technology support etc.
Has successfully applied its techniques to plant facilities in a large number of projects, both in Japan and overseas, and is praised from various perspectives by its customers.
Energy Saving Approach
1-1. Energy conservation by introducing GT exhaust gas into process heating furnace
It is energy-saving technology to just introduce thermal energy of the high temperature exhaust gas (500-550 degrees Celsius) of the gas turbine into furnace as the combustion air. Because it is enough for stable operation of the furnace and can largely reduce fuel consumption of the furnace because around 15% of oxygen remains in the exhaust-gases of the gas turbine, fuel reduction to furnace is higher than the fuel which is necessary for gas turbine combustion, and it is energy saving.
Technical introduction
In addition to fuel reduction of the existing furnace by the introduction of the high temperature gas Turbine Exhaust Gas (TEG), Chiyoda can suggest further fuel reduction by evaluating steam system configuration and steam balance of the customer. In the following example, further fuel reduction of the existing steam boiler is by collecting middle pressure steam from additional WHB using heat energy of the exhaust gas and by reducing the extracted steam flow rate of the extraction/condensing turbine for middle pressure steam collection.
To maintain the electric power generation of the extraction/condensing turbine generator, condensing water is increased to compensate decreasing quantity of extracting steam flow rate.

<Key Projects>
Customer : JXTG Nippon Oil & Energy Corporation in Negishi, Japan for EPC work
1-2. Factory energy system potential evaluation by R-curve analysis
Fuel is necessary to produce product in the factory. The heat of the fuel is converted into the heat supply that is necessary for the operation of the factory and electric power/driver power generation. Chiyoda can provide a lot of energy saving suggestion to customer using R curve analysis that indicates whether the heat of the fuel is utilized effectively, and how much of improvement room (potential) in your factory at first sight. Chiyoda has large number of energy saving suggestion results in oil refining, petrochemical plant mainly so far regardless of domestic and abroad.
Technical introduction
Chiyoda can provide a plain diagrammatic chart which shows potential improvement of energy efficiency of the heat of the fuel in your factory by analyzing customer provide actual operation datum of the factory.
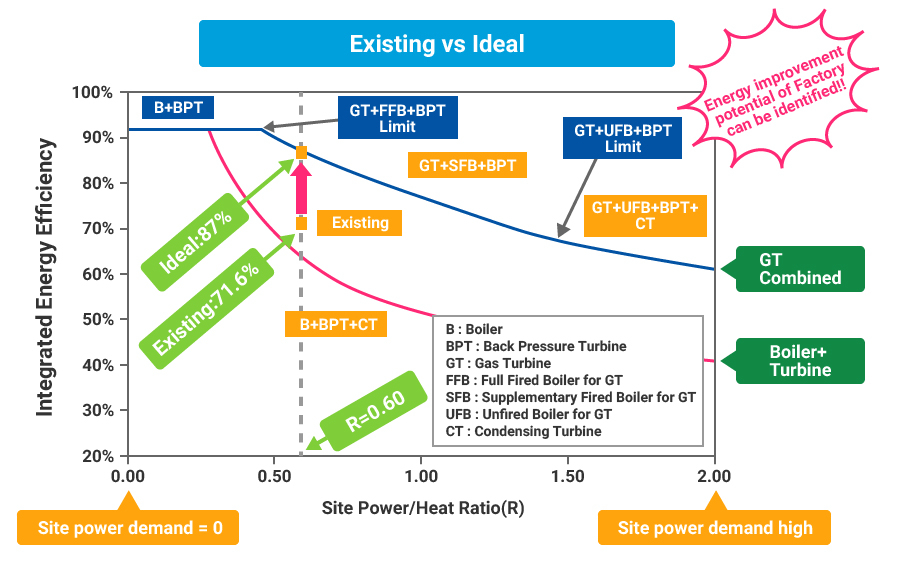
<Key Projects>
More than ten companies overseas and more than 50 companies domestic refinery and petrochemical
1-3. Low-temperature waste heat recovery power generation technology
The exhaust heat recovery power generation in factories uses steam cycle mainly, and generally the temperature targeted for the heat recovery is more than 250-300 degrees Celsius. For the waste-heat of lower temperature, heat recovery as low pressure steam was common. Chiyoda can perform suggestion of the power generation system introduction to use the waste-heat such as more low temperature waste-heat without being utilized and threw away until now in customer's factory by applying Kalina power generation (water - ammonia mixture as working medium) to generate electricity.
Technical introduction
The following is a basic flow of the Kalina power cycle. Because water - ammonia mixture (ammonium hydroxide) which is working medium of the Kalina power cycle has lower boiling point than water, the heat of the heat source is available to a low temperature range. It is heated up with an vaporizer by waste-heat, and the ammonium hydroxide becomes the wet steam and the ammonia vapor separated with a separator turns a turbine and generates electricity.
As for the tower top gas (around 120 degrees Celsius) of the distillation column cooled in air fin cooler as an example, heat of the tower top gas is thrown away to the atmosphere as waste-heat. Chiyoda has experience of introducing Kalina power cycle utilizing waste-heat (tower top gas).

<Key Projects>
Customer : Fuji Oil Company, Ltd. in Sodegaura, Japan for EPC work
1-4. Changing steam condensing turbine for driver of large compressor with variable speed motor
Because power generation efficiency of the steam condensing turbine used for the drive of a pump and the compressor is not so high, changing the steam condensing turbine to motor is energy saving for decreasing the condensing turbine drive steam→decreasing boiler generation steam → decreasing boiler fuel. In addition, it is connected for energy saving by condenser removal to become cooling tower load and cooling water pump load reduction.
Chiyoda has only one experience in Japan refinery for engineering, procurement, construction of changing the condensing turbine for the drive of large compressor to variable speed motor.
Technical introduction
Chiyoda analyzes actual operation datum of compressor of customer's factory in changing the steam condensing turbine for driver of the compressor to variable speed motor whether a compressor does not have any problem from starting to normal driving, decommissioning, and run safely, and reflect it design.
Chiyoda plans construction of removal, remodeling, new establishment of the associated facility such as equipment, electricity, instrumentation, and perform safely within a period and accomplish it.

<Key Projects>
Customer Seibu Oil Co,.Ltd. in Yamaguchi, Japan for EPC work
Environmental Improvement

Chiyoda, in aiming for harmony between enegy and environment, offers suggestions to the environmental issues in your plant.
With our proprietary technology in the field of air and water pollutant control, Chiyoda can provide ways for plants to manage their industrial waste.