装飾1
装飾2
装飾3
Enriching Society
through Engineering
Value
News
Latest News-
Press Release
Chiyoda Corporation Awarded an EPC Contract by Saibu Gas Co., Ltd to Enhance the Capacity of their Hibiki LNG Base
-
IR Information
Transcripts and Q&A from Conference Call, August 4, 2025
-
IR Information
Financial Results for 1Q, FY2025
-
Information
Encouragement to take Annual Paid Leave on August 12, 2025
-
Information
Digital signage advertising will be launched at Yokohama Landmark Tower [July 14 - August 10]
装飾1
Engineering
New Social Value
New Social Value
FUTURE
装飾2
装飾1
Addressing Diverse
Social Challenges
Social Challenges
BUSINESS
装飾2
装飾1
Leveraging Our
Strengths
Strengths
ADVANTAGE
装飾2
装飾1
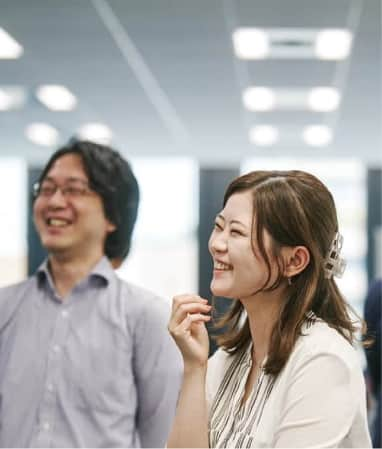
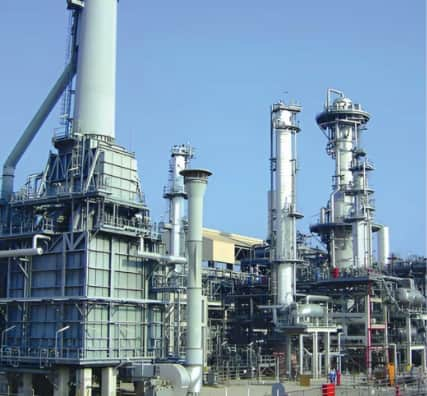
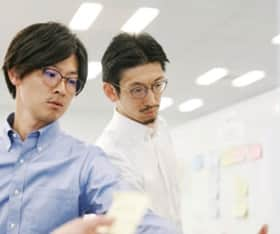
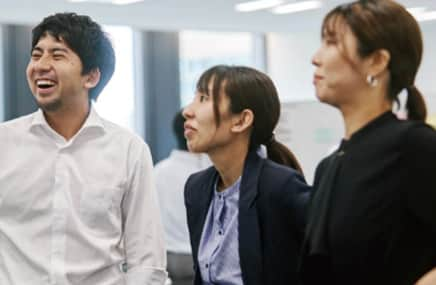
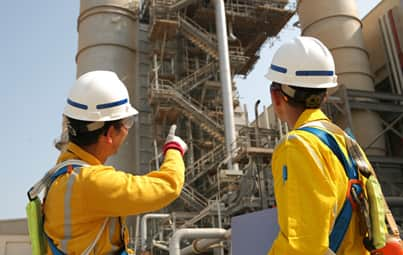
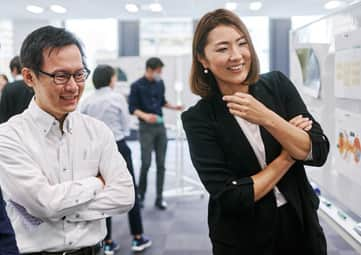
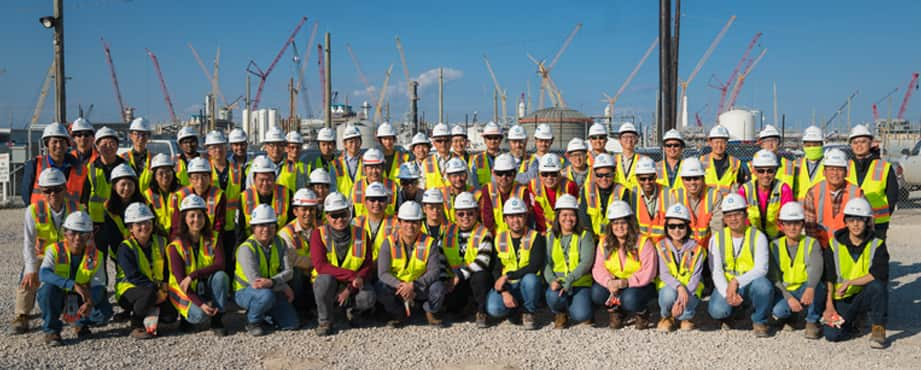
Together with
Society
Society
装飾2