Floating LNG Power Vessels
As an LNG value chain solution, a Floating LNG Power Vessel is a floating power generation unit using LNG as fuel.
The Floating LNG Power Vessel fulfills four functions:
- LNG Loading Facility
- LNG Storage
- Regasification
- Gas Fueled Power Generation
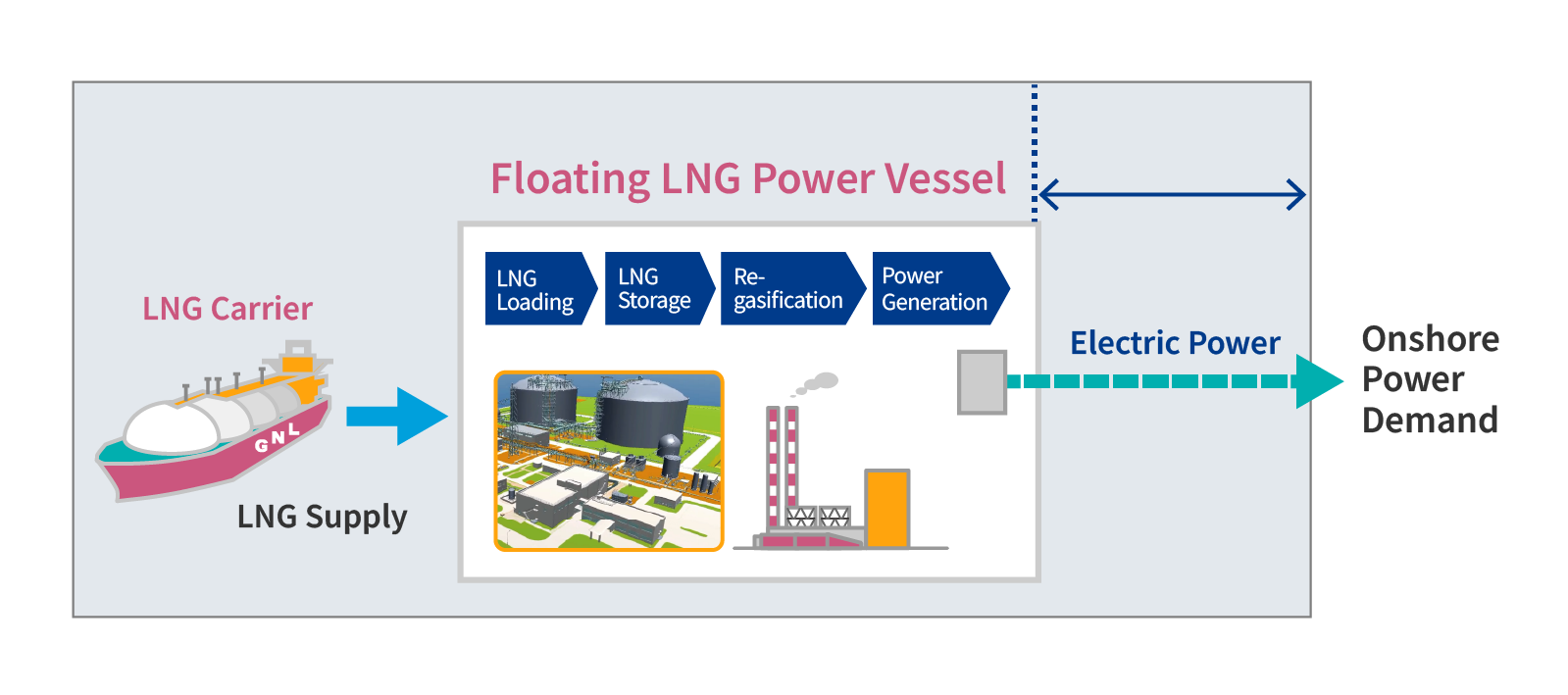
Overview
Chiyoda offers Floating LNG Power Vessels for small to medium-scale power generation systems with the four functions.
Power Generation System
- Small Scale: Gas Engine (Dual Fuel Diesel Engine) Generator System
- Medium Scale: Gas Turbine Combined Cycle
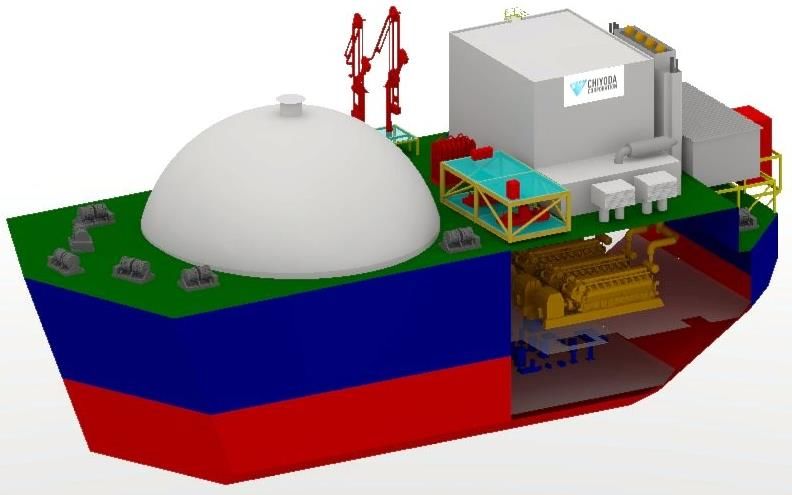
Capabilities
Key design considerations are as follows:
1.Reliable Design and Operation
Chiyoda has constructed the majority of domestic liquefied natural gas (LNG) receiving terminals and is a market leader in the construction of LNG liquefaction facilities worldwide. Chiyoda’s LNG project experience and capabilities ensure reliability in design and operation, including LNG handling and utilizing systems of Floating LNG Power Vessels. Because the vessel is a floating unit, equipment and systems comprise proven technologies in marine and offshore industries, providing reliable Floating LNG Power Vessels.
2.Safe Design
Safety is a core Chiyoda value and is a priority in floating vessels. Our strong safety track record in plant design and construction also extends to the safe design of Floating LNG Power Vessels. Chiyoda’s Floating LNG Power Vessels segregate hydrocarbon and non-hydrocarbon systems and supporting utility systems by area. Chiyoda’s Floating LNG Power Vessels concept design received Approval in Principle from the American Bureau of Shipping (ABS) in May 2016.
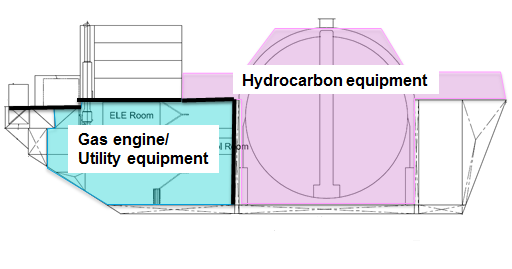
3.Low Cost & Short Delivery Time
A key feature of Chiyoda’s Floating LNG Power Vessels is the ‘conversion’ concept, whereby the Floating LNG Power Vessel is converted from a redundant LNG Carrier, enabling ‘Low Cost’ and ‘Short Delivery Time’ Floating LNG Power Vessels.
The main features of the conversion concept are:
- Any Cargo Containment System (Moss, Membrane and SPB) can be adapted to a Floating LNG Power Vessel using Chiyoda’s conversion concept.
- One LNG Carrier can be converted into several Floating LNG Power Vessels (depending on the number of tanks of the donor LNG Carrier and/or the output power capacity of the Floating LNG Power Vessel)
- LNG tank and hull in way of LNG tank of donor LNG Carrier will be used to Floating LNG Power Vessel as LNG storage and surround hull structure.
- Additions and modifications:
- A dual fuel diesel engine or gas & steam combined cycle turbine generator is installed for electrical generation.
- A new deck house and machinery spaces in the aft/forward structure is fitted for newly installed equipment space and stability.
- The existing hull, machinery and materials are refurbished accordingly.
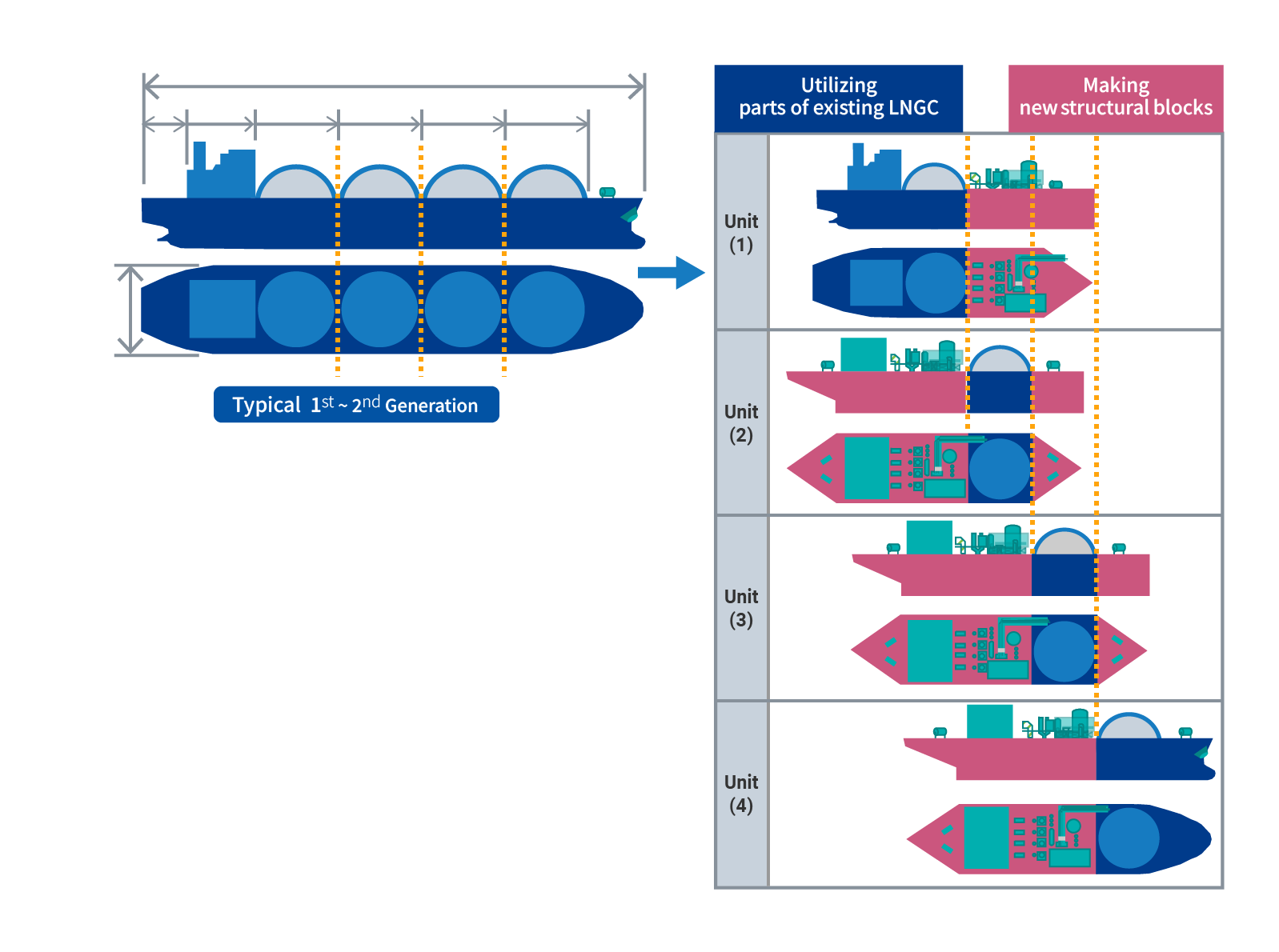
Applicable Range
The Floating LNG Power Vessel is suitable for the following areas or purposes:
- Environmentally conscious and/or high electricity demand areas.
- Remote areas away from mainland/cities with low electrical demand, eg: small islands.
- Areas with poor electrical power supply facilities and requiring early response.
- Areas adjacent to large LNG supply facilities.