Petrochemical / Chemical
The petrochemical industry produces chemical products such as polymers, fibers and rubber from raw materials using many different processes including petroleum, LPG, natural gas and other hydrocarbons. As a source material, hydrocarbons produce components such as ethylene, propylene, butadiene and pyrolysis gasoline through non-catalytic thermal decomposition reaction with steam (steam cracking). The feedstock for the ethylene process depends on the national availability of resources and naphtha (crude gasoline), produced by refining crude oil, is often used in Japan.
Chiyoda’s expertise in the petrochemical and chemical industry is shown below by source material classification:
[ Overview of the Petrochemical and Chemical Industry ]
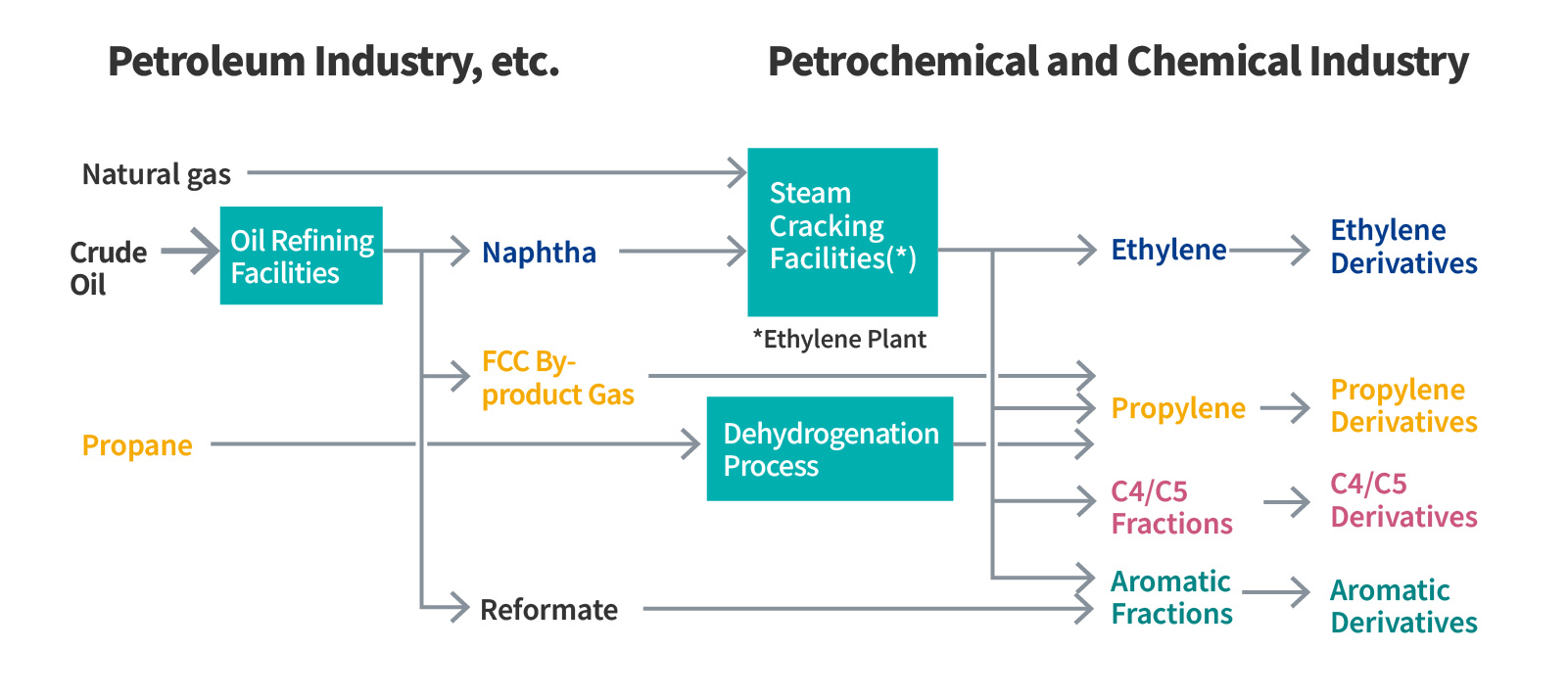
The petrochemical and chemical industry utilizes significant quantities of carbon dioxide (CO2) as a resource. Chiyoda continues contributing towards carbon neutrality through heat source conversion, raw material conversion and recycling and leveraging experience accumulated through the construction of petrochemical and chemical plants, providing battery materials and components and accommodating the needs of semiconductor-related plants.
Key Business and Technology
Key Projects
Chiyoda has participated in the design and construction of domestic and overseas ethylene plants and downstream petrochemical and chemical facilities since the 1960s. Since the 1980s, we have constructed larger-scale petrochemical and chemical plants worldwide as customers ‘upsized’ their plant requirements. We successfully completed the world's largest (at that time) ethylene plant with an annual production capacity of 1.8 million tons in Texas, USA in 2021.
[ Block Flow of Ethylene Plant ]
![[ Block Flow of Ethylene Plant ]](/service/img/chemistry02_e.jpg)
A key feature of petrochemical and chemical plant technology is the extended and complex processes required for the removal and refining of product materials, due to the by-products generated from the reaction process, requiring specialist equipment and operation. Chiyoda’s extensive petrochemical and chemical plant simulation, analysis, engineering design and construction expertise includes bulk chemical plants with annual production capacities of 0.1 to 1 million tons such as ethylene plants, to general chemical plants within annual production capacities of over ten thousand tons.