装飾1
装飾2
装飾3
Enriching Society
through Engineering
Value
News
Latest News-
Press Release
Chiyoda Corporation Concludes MOU with Ekwil S.A.S Regarding Collaboration on the Floating Offshore Wind Turbine Project in Japan
-
IR Information
Date of Announcement of the Financial Results for the 1st Quarter of the Fiscal Year Ending March 31, 2026
-
Press Release
Chiyoda Corporation and AVEVA Forge Strategic Partnership to Power plantOSTM*1 with AVEVATM CONNECT
-
IR Information
Notice of Resolutions at the 97th Ordinary General Meeting of Shareholders
-
IR Information
(Updated on Disclosed Matters 7) Current Status of the Golden Pass LNG Project in the U.S.
装飾1
Engineering
New Social Value
New Social Value
FUTURE
装飾2
装飾1
Addressing Diverse
Social Challenges
Social Challenges
BUSINESS
装飾2
装飾1
Leveraging Our
Strengths
Strengths
ADVANTAGE
装飾2
装飾1
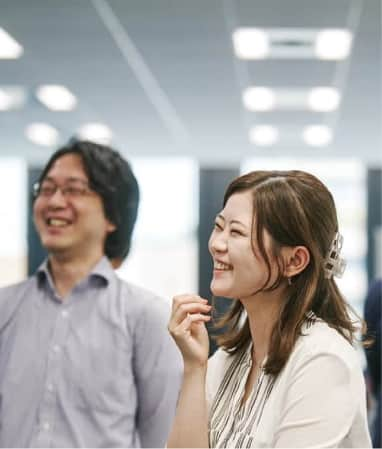
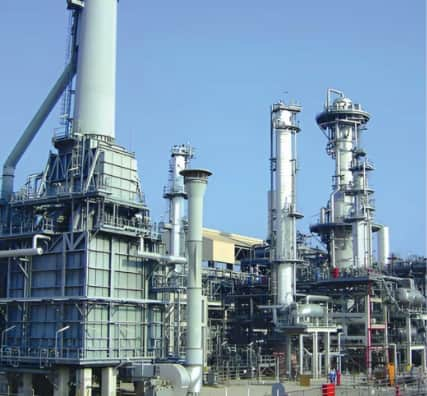
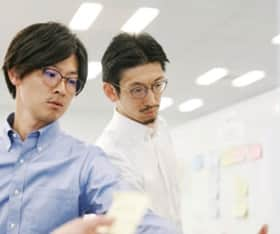
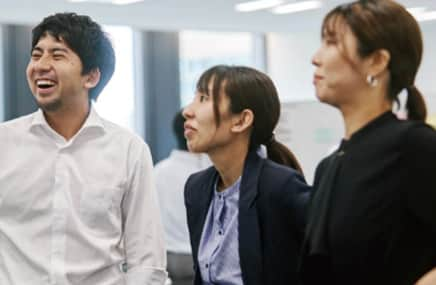
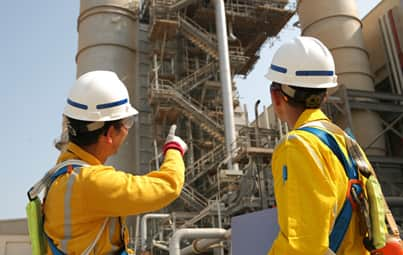
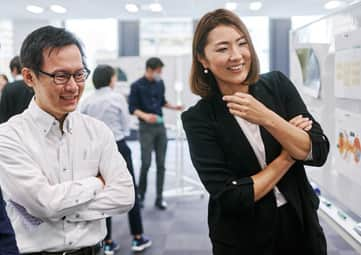
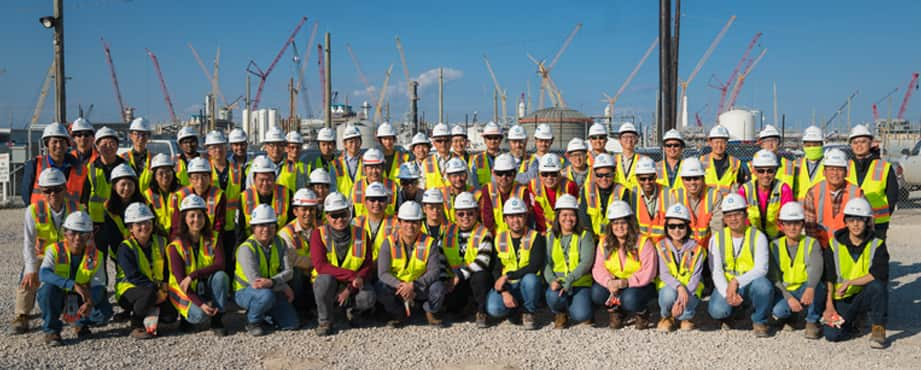
Together with
Society
Society
装飾2