装飾1
装飾2
装飾3
Enriching Society
through Engineering
Value
News
Latest News-
Information
Digital signage advertising will be launched at Yokohama Landmark Tower [July 14 - August 10]
-
Press Release
Chiyoda Corporation and Ekwil Awarded Feasibility Study of Floating Offshore Wind Turbine Project in Japan
-
Press Release
Development of Large-scale Production Technology for Useful Proteins Using Plants
Launch of a 'Plant Biofoundry' - a Demonstration Platform in the Field of Bio-manufacturing -
Press Release
Announcement of Wage Increase for Fiscal Year 2025
-
Information
Encouragement to take Annual Paid Leave on July 18, 2025
装飾1
Engineering
New Social Value
New Social Value
FUTURE
装飾2
装飾1
Addressing Diverse
Social Challenges
Social Challenges
BUSINESS
装飾2
装飾1
Leveraging Our
Strengths
Strengths
ADVANTAGE
装飾2
装飾1
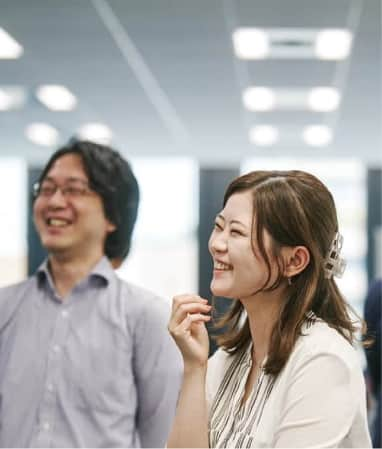
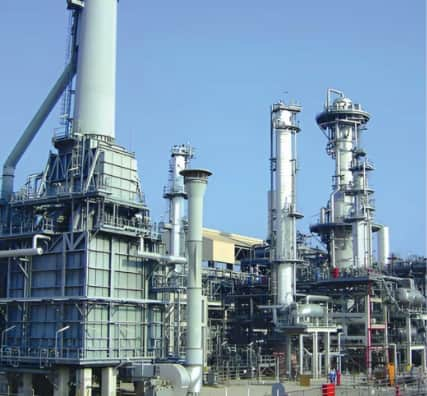
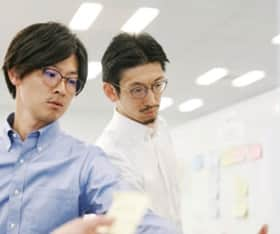
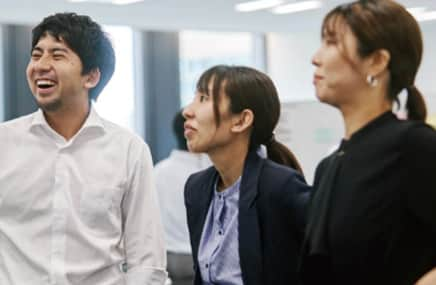
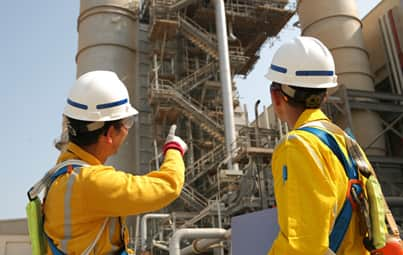
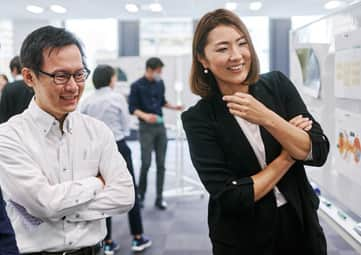
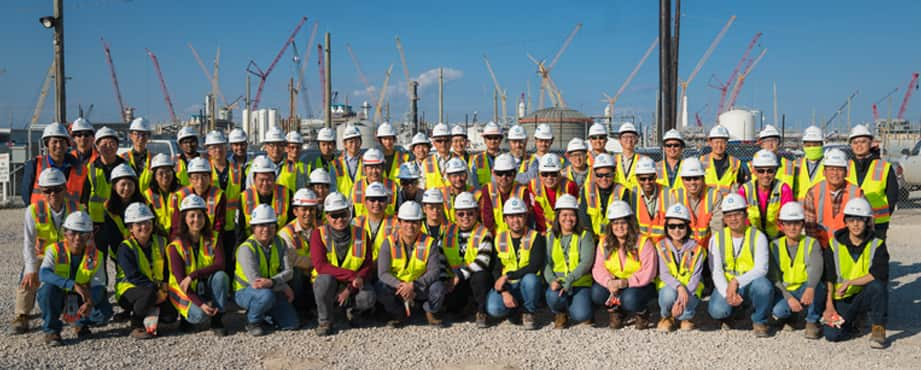
Together with
Society
Society
装飾2